「リーン開発」という言葉でネット検索をすると、ほとんどのものが「リーンソフトウェア開発」または「アジャイル開発」ということになります。
また、「リーン」という言葉は、トヨタのかんばん方式を連想させトヨタの開発方式として捉えられたり、トヨタの開発現場から来たソフトウェア開発手法という言い方をしている人までいます。
また、ちょっと経営よりな考え方としてエリック・リースの書いた「リーンスタートアップ」という本もあります。
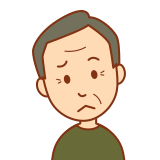
リーン生産はあまりにも有名ですが、リーン開発って日本ではあまり使われていないんです。トヨタの開発方式ということなんですが、トヨタも特別なことをやっている意識はないようですね。
実は、私が取りあげたいのは、「リーン製品開発」というソフトウェアに限らない製品開発の本質的なアプローチです。
この本は、リーン製品開発ということを、非常にわかりやすく実例を小説のように仕立てて説明してくれます。
著者の稲垣公夫さんは、私が以前勤めていたジェイビルサーキットというアメリカのEMS企業で日本法人の社長をしていたかつての上司なのですが、もともとは生産系の方でトヨタのかんばん方式などの書籍を翻訳されたりして、リーン生産に詳しい方です。
この本を書く前に、アメリカの書籍を翻訳される中で、開発に関する面白い本があるよ、と言って私に「リーン開発」について説明してくれたことがあるのですが、「要素開発でトレードオフを徹底的に詰めて設計パラメータを決めていく画期的な手法のようなんだ。」と言われ、
「稲垣さん、それは開発では当たり前にやってることですよ。」
というのが、私の最初の反応でした。
実は、このことがとても大事なことなのですが、多くの日本企業の開発マネージャさんや、経営層と言われる方も、この話をすると「そんなの当たり前にやってるよ。」というのが最初の反応なのです。
トヨタの「リーン製品開発」は、1990年代に、ミシガン大学のアレン・ウォード教授がトヨタのやっている製品開発手法のすごさに気づき、研究メンバーを派遣して開発方法を学び、アメリカに持ち帰って体系化したものと言われています。
その後、アメリカでは10冊前後の本が出版されて広まっていきます。日本のTQCで自動車や家電製品などで日本の後塵を拝したアメリカは、その後、日本に追いつけ追い越せと日本を学ぶことから始めて、マルコム・ボルドリッジ賞で日本を逆転していく時期とも一致して、多くのアメリカ企業がこの手法を取り入れて元気になっていきます。
稲垣さんの本の中にも出てきますが、テラダインペソスという会社では、会社の立て直しにこの手法を独自のものとして消化し、「Knowledge Base Development」という考え方で業績を拡大させています。(この本は非売品です。)
私も稲垣さんといっしょにボストン郊外にあるこの会社を訪問し、この本を書いた開発本部長のBob Melvinさんにお会いし、新入社員向けにやっている「knowledge base development」の研修を紹介してもらいましたが、開発の本質に根差した基本的な考え方を若い人に植え付ける、非常に効果的な研修方法になっています。
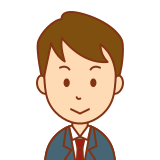
Bobさんの熱意はすごかったです。この本でも言ってますが、理想的なプロセスを理解するだけではダメで、現実の泥臭い世界にどうやって実現させるかがとても苦労したそうです。
日本では、稲垣さんが翻訳された「トヨタ製品開発システム(モーガン、ライカー共著)」が唯一の本でしたが、上記の「開発戦略は意思決定を遅らせろ!」を皮切りに、少しずつ見直されてきています。
しかしながら、日本での普及を邪魔する一つの要因が、「それはやってるよ。」ということなのです。
「リーン開発」手法で言っていることは、
- 顧客が何を望んでいるかをきちんと捉える
- 顧客の要求に対して、自分たちの現状(知識)と要求到達のための知識ギャップを把握する
- 知識ギャップを埋めるためのトレードオフを小さな実験で掴む
- トレードオフと、顧客要求とを考慮して、関連者全員でパラメータを決定する
という、一見すると誰もが納得できる「当たり前のこと」なのですが、例えば2の知識ギャップの認識なども、自分たちのポジションを客観的に掴むこと、自分の知らないことをきちんと認めることの難しさは、多くの開発者たちが甘く考えてしまい罠にはまりやすいポイントです。
さらに、3のトレードオフを小さな実験で、というところは、多くの日本企業が省略してしまい、特性を把握しないで一点突破の設計をして、泥船の試作機をデバグしては後戻りするという悪循環に陥る元凶になっています。
しかし、多くの設計マネージャーや経営者は、この理想の考え方があることを知っています。そして、この理想的な手法を基本的には自社でもやっていると信じています。
現場で実際に起こっていることと、この理想の手法とのギャップがあることに気付いていたとしても、それは致命的なことではないと考えてしまうのです。
日本企業は高品質、大量生産という切り口でかつて大成功を収めてきました。
営業チャネルから流れてくる既存顧客の要求を次機種の企画に反映していれば、会社の繁栄は永遠に続くものと大きな誤解をしているのです。
アメリカ企業が、日本に負けまいと日本から学ぼうとする姿勢が、今、日本にはないように思えます。
真摯に自分たちの現状、出来てないこと、知らないことを認めて、それを学んでいくことが大切です。ひざ元の日本のトヨタで行われていたことを、なぜアメリカ人が持ち帰って体系化された手法にしてしまったか、日本のトヨタ以外の企業が学べなかったのはなぜかを考えていきたいと思います。
実は、もう一段問題点があって、トヨタに学んでトヨタの「チーフエンジニア制度」や「A3資料」のような表面的なことを真似して安心している企業も多く見受けられます。
その本質を理解しないで、表面的な制度だけを作っても意味がありません。
理想論は理解できている。では、現状とのギャップはどうなっていて、そこに到達するためにはどうするか。というのは、このこと自体がリーン開発の重要なプロセスでもあります。
現場と理想論のほんのちょっとの、でも本質的なギャップを掴むことから、日本企業の再生が始められると思っています。
リーン製品開発の基本的な流れは、別記事「トヨタ式リーン製品開発とは」を参照ください。
また、半日のセミナーで、リーン開発手法の理論、導入事例、自社への展開法をお伝えしています。
コメント